Sepas holding and Drill-AI , in Cooperation with Sharif University of Technology Present:
“The Role of AI in Oil & Gas industry”
Smarter Drilling With AI
Unlock the power of AI with DrillAI’s intelligent modules—each designed to optimize a specific part of the drilling process .
We combine AI, data science, and field experience to reduce time and cost by turning complex data into clear, cost-saving actions
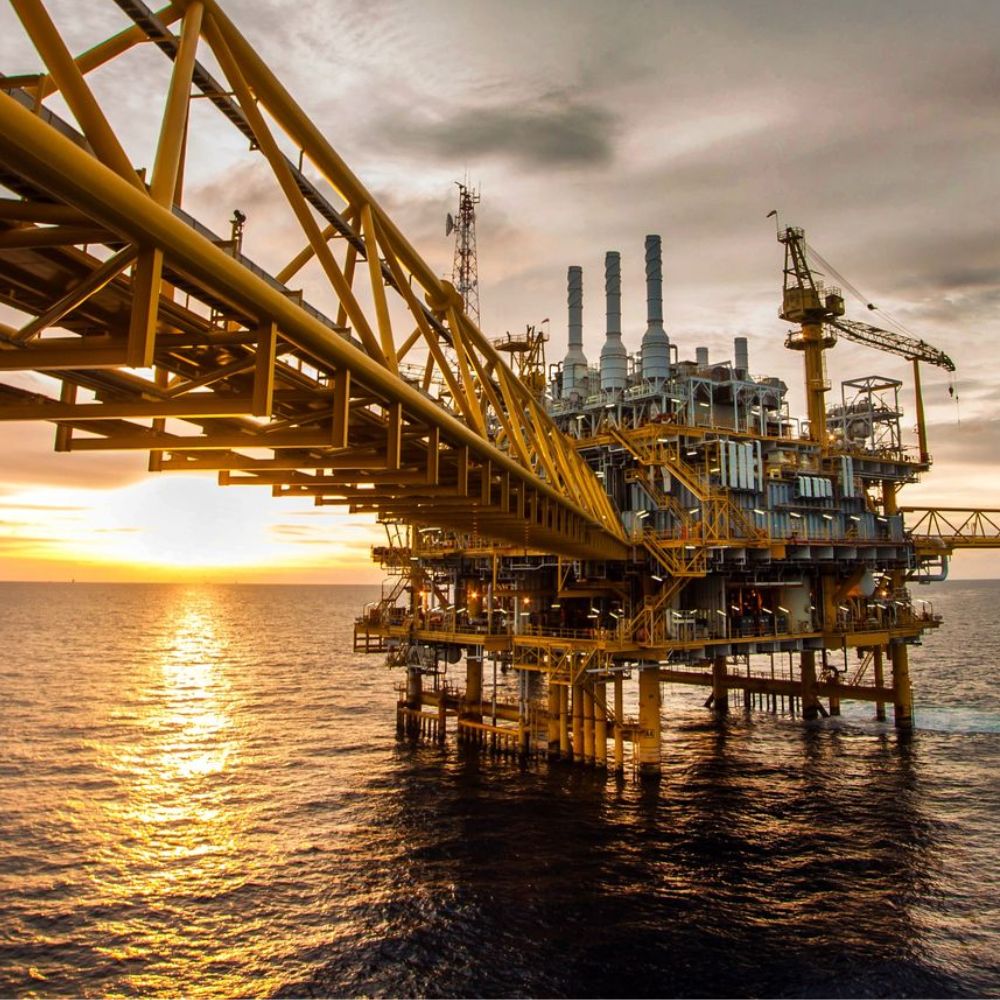
- Cross-Platform Module
Every company can use our product on all platforms including desktop, web, and mobile. Moreover, they can use them as Web API services.
- Data-Driven and AI-Based Module
In addition to the traditional methods which had been used in oil and gas industry Module, high-tech methods such as data science and artificial intelligence are being used in our products.
- Integrated oil and gas industry Module
All Data-Driven and AI-Based Module in different fields of the oil and gas industry such as drilling, reservoir, and production are being developed by the DrillAI team.
- What is DrillAI?
With a strong emphasis on Artificial Intelligence, Machine Learning, and Data-driven methods, DrillAI is at the forefront of technology and is dedicated to create and develop cutting-edge software for challenging and costly operations in the Oil and Gas industry.
Our team of experts harnesses the power of AI and Data to optimize exploration, drilling, production, and operational processes, resulting in increased efficiency and cost-effectiveness.
By leveraging advanced and sophisticated technologies, we enable our clients to make data-driven decisions, improve operational performance, minimize costs and maximize profitability.
With our innovative solutions, we aim to revolutionize the oil and gas industry, driving growth and sustainability.
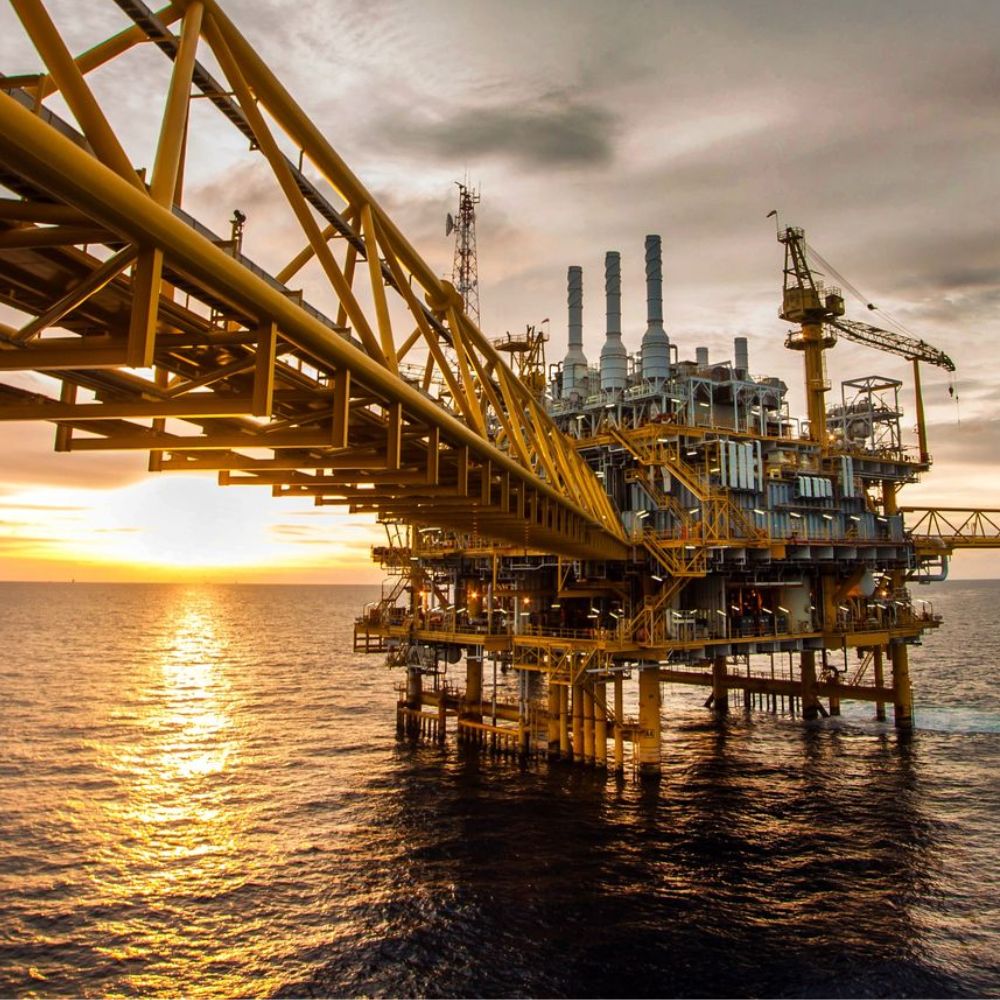
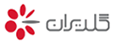
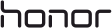
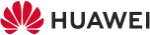


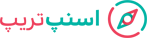
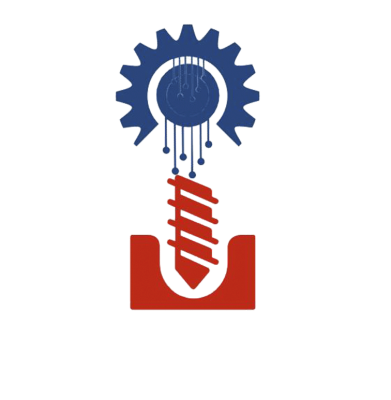
Our Mission
Our mission is to revolutionize the Oil and Gas industry through the power and innovation of Artificial Intelligence to drive the oil and gas industry towards a more sustainable and profitable future.
Our goal is to transform the Oil and Gas industry by enabling our clients to leverage the latest AI technologies and the power of data to solve their biggest challenges and reach the best possible results, make better decisions, improve safety, decrease costs and increase profitability.
We strive to be at the forefront of AI research and development, continually pushing the boundaries of what is possible in the industry and we envision a world where our AI solutions are widely adopted by Oil and Gas companies of all sizes.
- Transforming Oil & Gas with Artificial Intelligence
- Empowering Smarter Decisions and Greater Profitability
- Pioneering AI Innovation for a Sustainable Future
- Driving Safety, Efficiency, and Growth Through Data
our services
Providing services based on your greatest needs
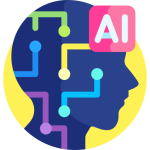
Stuck-Pipe Prediction and Prevention Module
Prediction and prevention of drilling string sticking to avoid wasting time and money using data-based methods
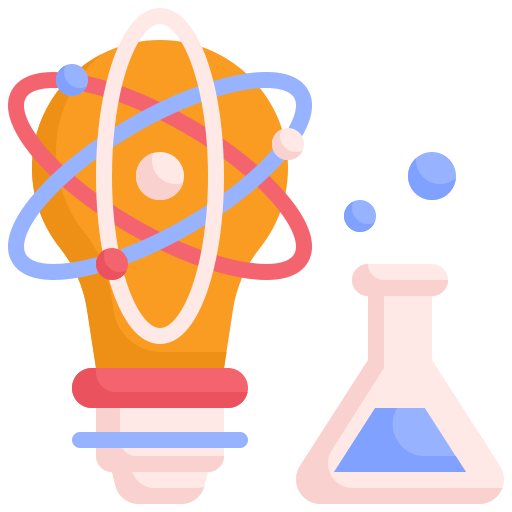
Data Preparation and Integration Module
collecting, structuring and cleaning data. Prepares raw data for furter processing
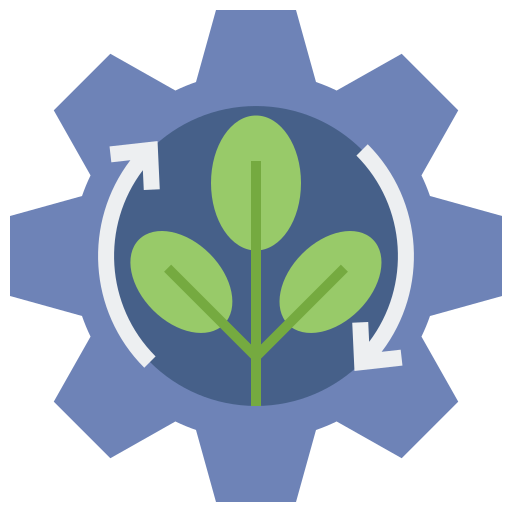
ROP Prediction and Optimization Module
predict ROP and find optimum drilling controlable conditions for faster drilling using intelligent methods based on offset wells data
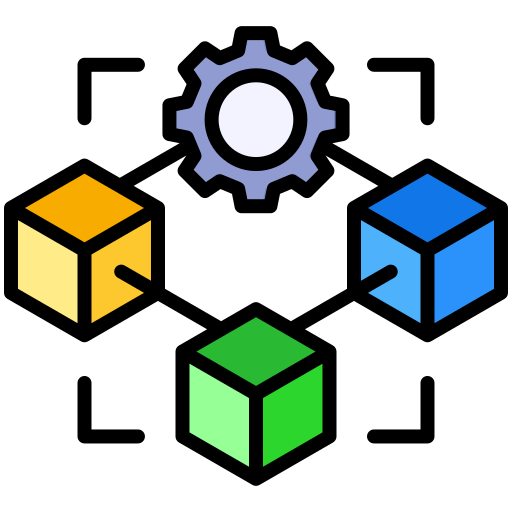
Pore Pressure Prediction Module
pore pressure prediction by deploying artificial intelligence to design better drilling plan and avoid operational problems
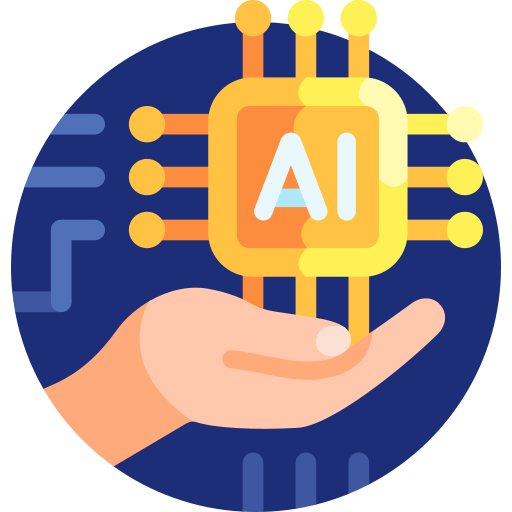
Rock-type and Lithology Detection Module
Detection of the lithology of the formation being drilled at each stage to prevent loss of production efficiency
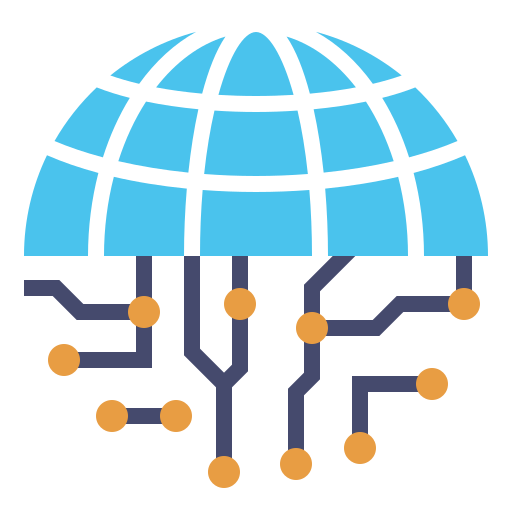
Vibration Detection and Prevention Module
Prediction of drill string vibration to have smooth and optimum drilling conditions, avoid vibration conditions, optimize the drilling procedure, and maintain the rate of penetration (ROP)
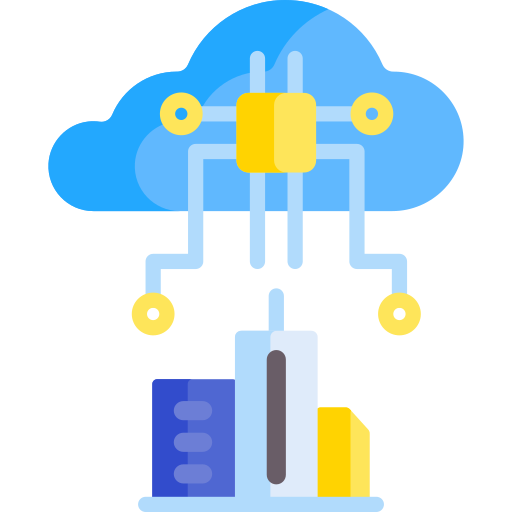
Hole Cleaning Prediction and Optimization Module
Hole-cleaning predictions in underbalanced drilling techniques (air drilling, foam drilling, etc.) aim to minimize formation damage, bit and stabilizer issues, and other drilling problems.
پشتیبانی ۲۴ ساعته، ۷ روز هفته | شماره تماس: 02159528
اپلیکیشن صرافی آنلاین تی پی !
با نصب اپلیکیشن به راحتی هر چه تمام و بدون واسطه خرید و فروش ارز های دیجیتال انجام دهید!
- ارایه خدمات در بستر آپلیکیشن های اندروید IOS و ربات تلگرام
- دسترسی به تمامی تراکنش ها و سفارشات شما
- اطلاع لحظه ای از قیمت تمام ارزهای الکترونیک و دیجیتال
- احراز هویت آسان و ارسال تیکیت و پشتیانی ۲۴ ساعته
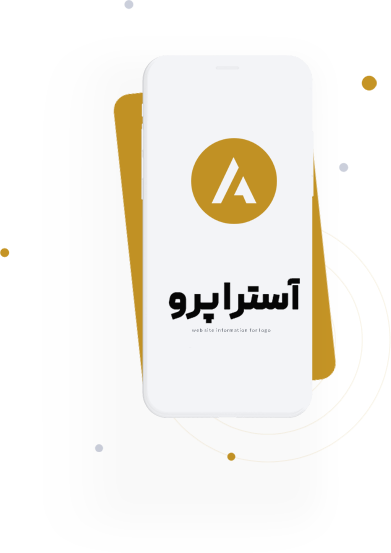